In the realm of electrical engineering and power systems, DC contactors serve as indispensable components that play a crucial role in controlling and managing direct current (DC) circuits. These electromechanical devices act as switches for DC power, allowing for the efficient and safe operation of various applications across different industries. Let’s delve deeper into what DC contactors are, their structure, working principles, and applications.
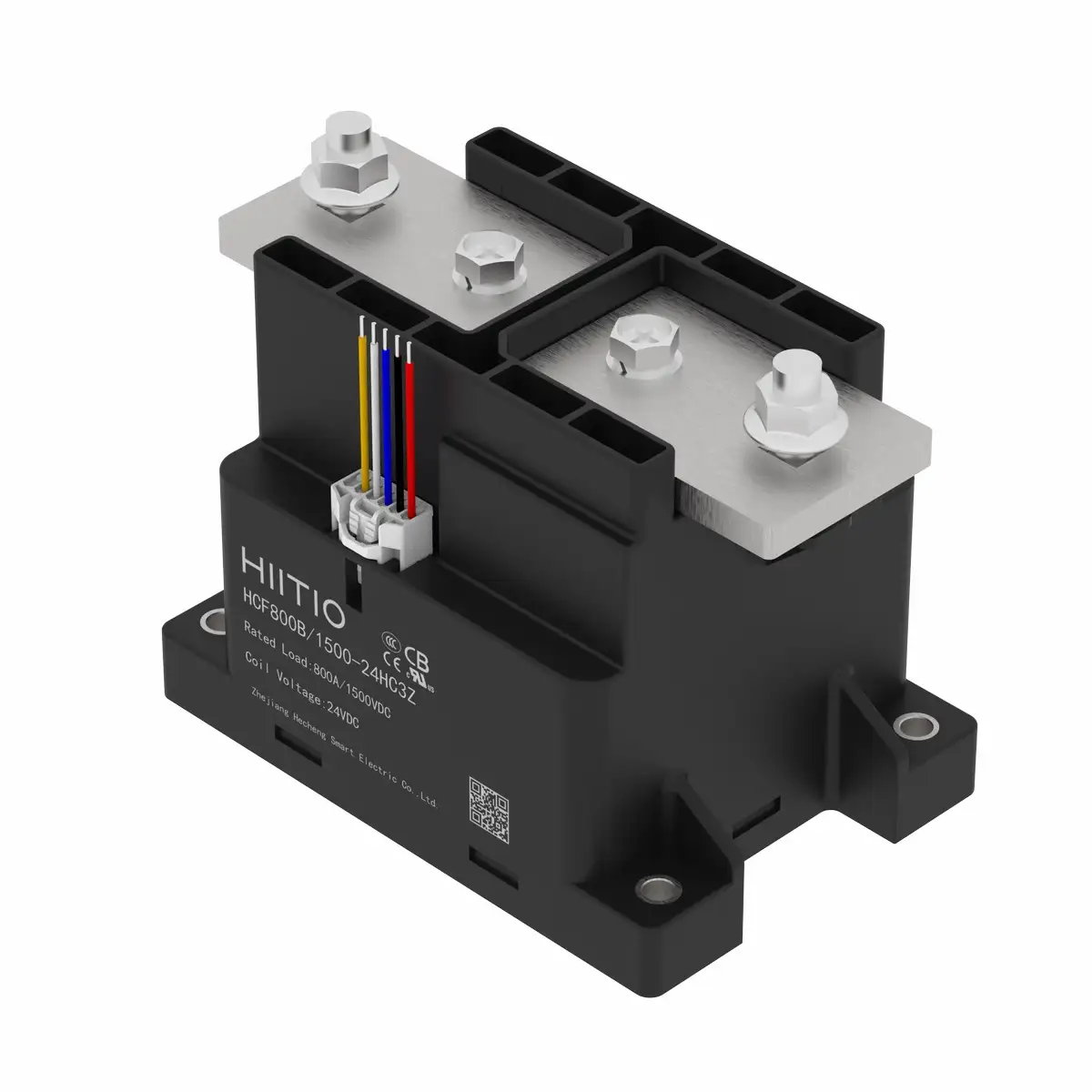
What’s a DC Contactor
DC contactors are essential electrical devices used in direct current (DC) circuits to control the flow of electricity. They function as switches, opening and closing the circuit to allow or interrupt the current flow. Unlike AC contactors designed for alternating currents, DC contactors are specifically engineered to handle the unique characteristics of DC power.
The Structure of DC Contactor
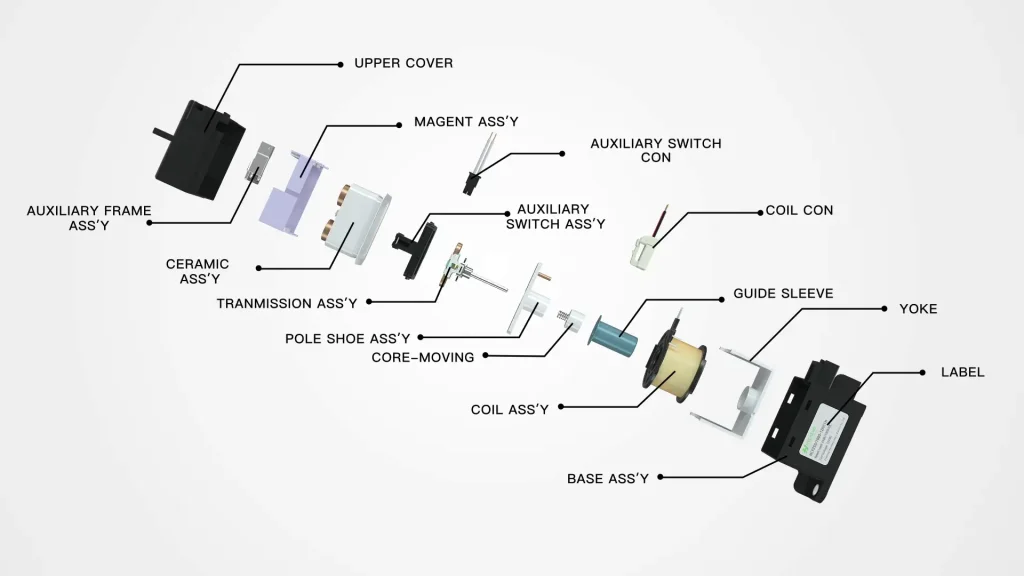
DC contactor consists of three parts: contact system, electromagnetic system and arc extinguishing system.
1. Contact System:
This component forms the core of the contactor’s current-carrying capability. It consists of the main contact and auxiliary contact, comprising fixed/static contacts, movable/dynamic contacts, and a shaft. When the fixed and movable contacts are apart, the circuit remains open (disconnected); when they come into contact, the circuit closes (connects).
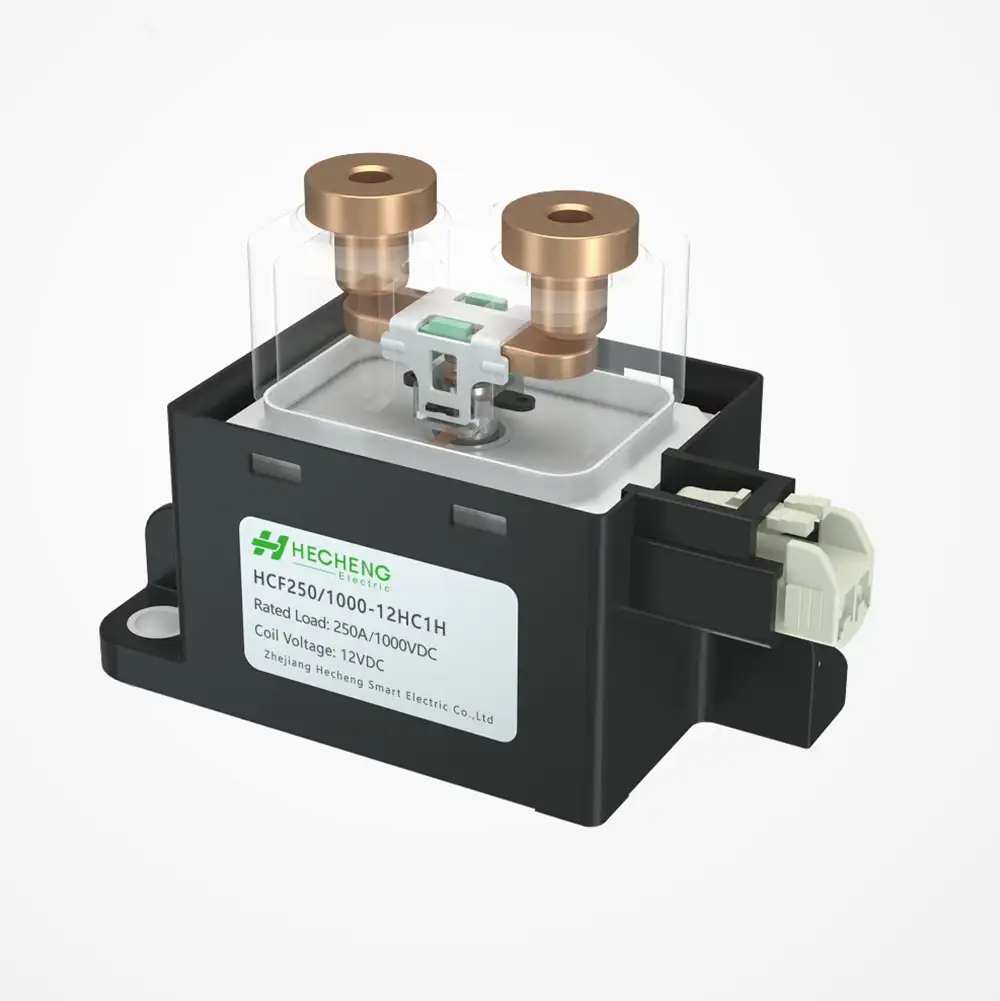
2. Electromagnetic System:
Comprising a coil, movable iron core, yoke iron, and magnetic conductive sheet, the electromagnetic system is responsible for generating the force necessary to close the contacts. The coil, also known as the electromagnet, creates the magnetic field required for contact engagement. The enclosure, typically made of insulating materials, houses the contacts and electromagnet, providing insulation and protection against accidental contact.
3. Arc Extinguishing System:
In high-current DC disconnections, the resulting electric arc can be challenging to extinguish. This system employs blowout coils to elongate and redirect the arc, facilitating faster and more effective arc extinguishing. The magnetic blowout arc-extinguishing equipment plays a crucial role in swiftly quenching the arc, ensuring safe and reliable operation.
HIITIO Resin High Voltage DC Contactors
HIITIO Ceramic High Voltage DC Contactors
Working Principle of DC Contactors
Contactor Excitation Process
When a control voltage is applied to a high-voltage DC contactor’s coil, it generates a magnetic field as current flows through the coil. This field causes the movable core (or armature) to move toward the fixed magnetic pole. As the armature moves, it pushes a mechanical lever or a set of contacts upward, closing the circuit and allowing DC current to flow through the power circuit.
Key Steps:
- Magnetic Field Creation: The coil generates a magnetic field when an excitation voltage is applied.
- Armature Movement: The armature is attracted towards the coil, causing mechanical movement.
- Contact Closing: The moving armature pushes the contacts closed, creating a current path in the circuit.
This process allows the contactor to conduct electricity, controlling high-voltage DC systems. The contactor is now in its “on” state, with the contacts closed and current flowing.
Contactor De-Excitation Process
When the control voltage is removed or the contactor is de-energized, the coil current stops, causing the magnetic field to collapse. As a result, the armature is no longer held in place by magnetic attraction. Instead, a mechanical spring or another return mechanism pushes it back to its original position.
Key Steps:
- Magnetic Field Collapse: When the current stops, the coil’s magnetic field fades away.
- Armature Return: A return spring or another passive mechanism pushes the armature back to its initial position.
- Contact Opening: The armature moves and pulls the contacts apart, interrupting the current flow and deactivating the circuit.
This de-excitation process turns off the contactor, stopping the current and isolating the high-voltage DC system.
Advantages of the Excitation/De-Excitation Process
Phase | Description |
---|---|
Excitation | When powered, the contactor creates a low-resistance path, allowing high-voltage DC current to flow and ensuring system control. |
De-Excitation | After de-energizing, the contactor cuts off the power supply, ensuring operational safety and protection against damage or faults. |
This excitation and de-excitation process is crucial for managing high-voltage DC circuits, ensuring reliable switching in industries such as renewable energy, electric vehicles, and industrial automation.
Applications of DC Contactors
DC contactors find extensive use across a wide range of industries and applications, including:
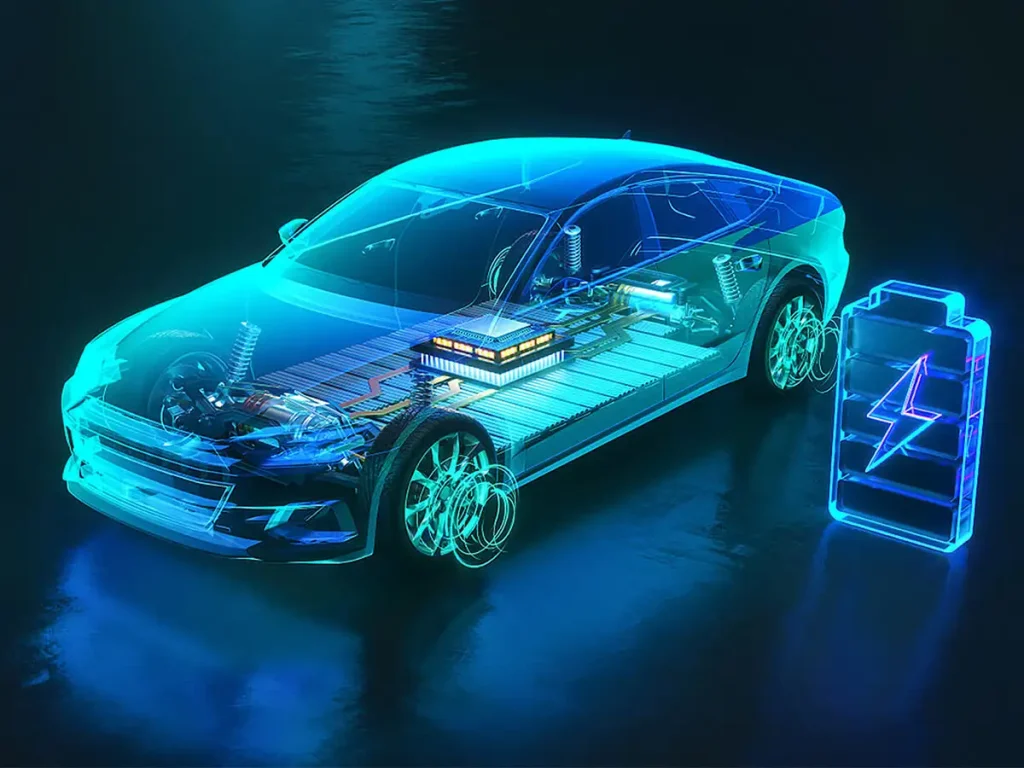
Electric Vehicles (EVs):
DC contactors are vital components in EVs, controlling the power flow between the battery pack and the electric motor. They ensure efficient energy management and safety during vehicle operation.
Electric Vehicle (EV) Charging Stations:
In EV charging infrastructure, DC contactors are used to control the charging process and manage power flow between the charging station and electric vehicles. They enable safe and efficient charging by providing isolation and switching capabilities.
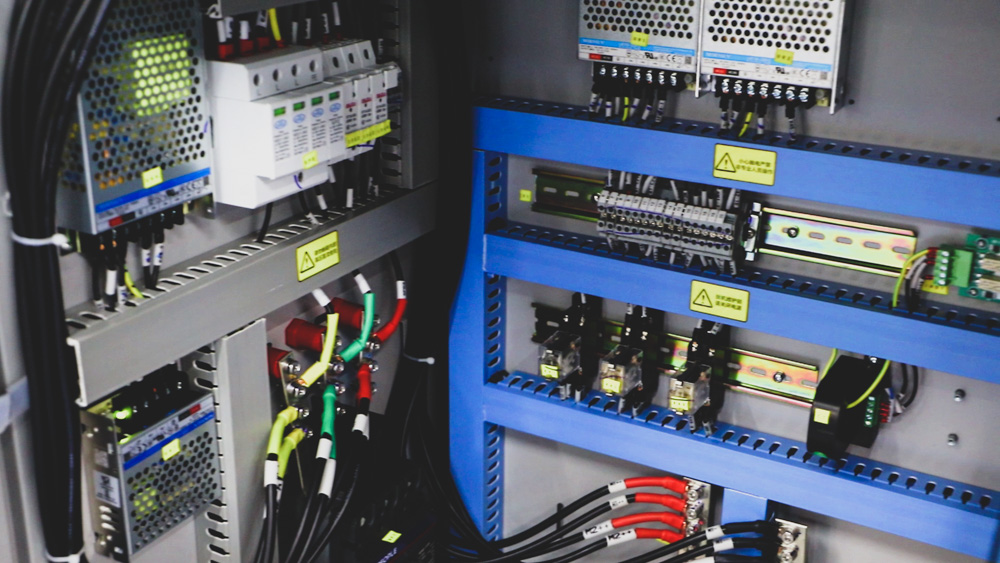
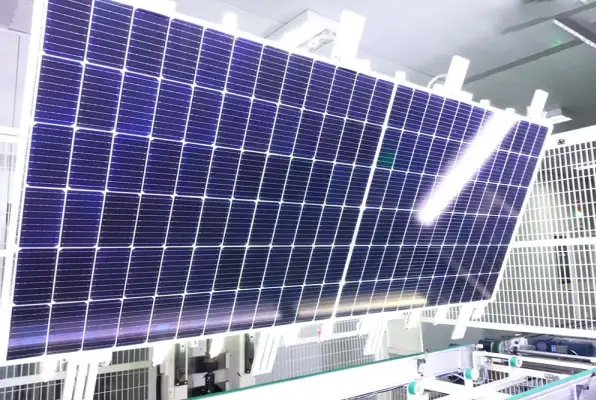
Renewable Energy Systems:
DC contactors play a crucial role in renewable energy applications such as solar power plants and wind farms. They are used in the connection and isolation of DC sources, ensuring smooth operation and integration of renewable energy into the grid.
Energy Storage Systems (ESS):
DC contactors are integral to energy storage systems, including batteries and supercapacitors. They facilitate the connection and disconnection of storage devices from the power grid, enabling efficient energy storage and utilization.
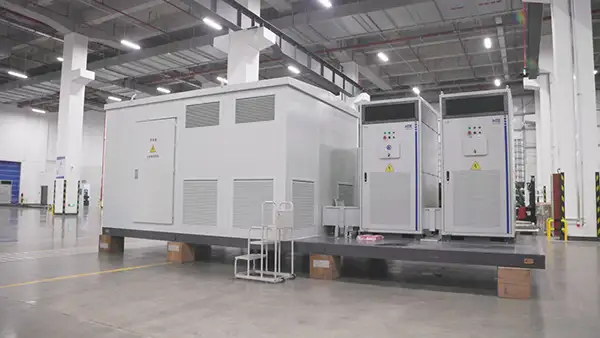
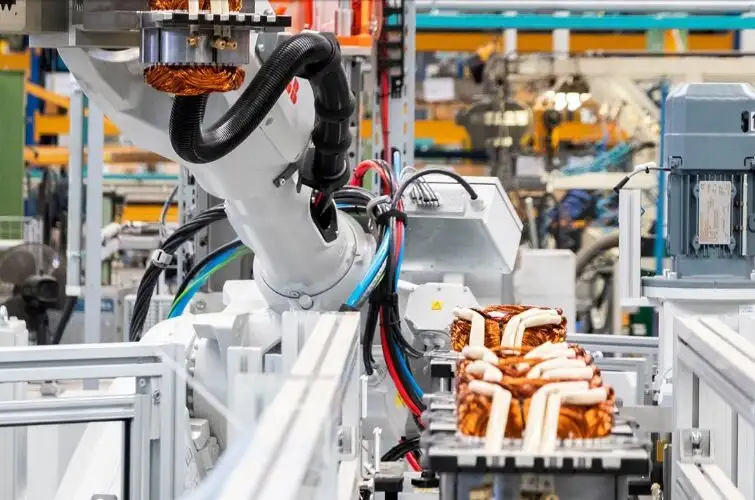
Industrial Automation:
DC contactors are integral to automation systems in manufacturing plants, robotics, and process control applications. They facilitate the control of DC motors, actuators, and other electrical loads.
HVDC Transmission Systems:
High-Voltage Direct Current (HVDC) transmission systems rely on DC contactors for switching and isolating DC circuits at high voltage levels. These contactors are designed to handle substantial currents and voltages for efficient power transmission.
5 Tips to Choose Suitable DC contactor
It may encounter various environmental conditions or unexpected accidents during the application of DC contactor. Therefore, it’s necessary to understand the performance and working conditions of DC contactor, or even test it under actual conditions to choose the suitable contactor for your application.
1. Coil
Pay attention to the coil’s polarity, nominal voltage, operating voltage, releasing voltage, working voltage, and coil resistance. Factors to consider include:
- The waveform of the control coil power.
- Voltage fluctuations and power supply stability.
- Ambient temperature, coil temperature rise, and hot start conditions.
- Voltage drop considerations when driving the contactor with a semiconductor
2. Main contacts
Evaluate the main contacts’ rated control capacity, contact resistance, and electrical life. Key points include:
- The size, type, and polarity of the contact load.
- Inrush current and switching frequency.
- The position and connection of the contactor within the circuit.
- Ensuring the contactor’s electrical life aligns with the equipment it supports.
- Ambient temperature considerations during operation.
3. Operate time
Understand the contactor’s operation time (close), bounce time (open), and release time (open). Factors to consider:
- The impact of actual temperature and coil voltage on these timing parameters.
4. Mechanical characters
There are 4 aspects to consider as: Vibration resistance, shock resistance, environment and mechanical life.
- Vibration and shock conditions during use.
- Altitude, temperature, and environmental contaminants (e.g., sulfur gas, oil, silicon-based substances).
- Potential magnetic field interference in the operating environment.
5. Other characters
In addition to the above, pay attention to insulation resistance, dielectric strength, installation procedures, and the physical size of the contactor. Key considerations:
- Ensure the installation torque of the main contact, and mounting base falls within specified ranges.
- Check the flatness and smoothness of the mounting contact surface.
- Implement anti-loose measures during installation to prevent issues.
Conclusion
DC contactors operate primarily through excitation and de-excitation processes, enabling efficient switching of high-voltage DC circuits. The transition between “on” and “off” states involves electromagnetic forces and mechanical components, ensuring precise power control. This functionality is essential for applications such as electric vehicles and renewable energy systems.
Their efficiency and rapid response times enhance electrical infrastructure, leading to a safer and more reliable future for high-voltage DC applications.
For further inquiries and in-depth knowledge about DC contactors, you can contact the HIITIO R&D team.